Bring your process into the IoT future
The Logiscend Container and Asset Tracking Application ensures you know where all your materials are at any time during the process — in real time.
Container and Asset Tracking
Know where your assets are in real time, count them, and record their status and attributes
The Panasonic Logiscend Container and Asset Tracking Application ensures you know where assets are at any point in the process.
- Track asset location and disposition
- Easily import list of assets and locations
- Set alarms or events for activity or maintenance
- Track and report asset history and management
– Downloadable reports into .xls format or
view in window - Compatible with fixed or handheld readers
- Enroll assets, take inventory or locate assets in the field and sync with main application
- Highly scalable application, expand for multi-location or multi-user capability
- High accuracy Real Time Location System (RTLS) with Bluetooth Low Energy (BLE) tags
- Create your own geo-fences and work zones to enable optimized tracking and triggering of automated workflows
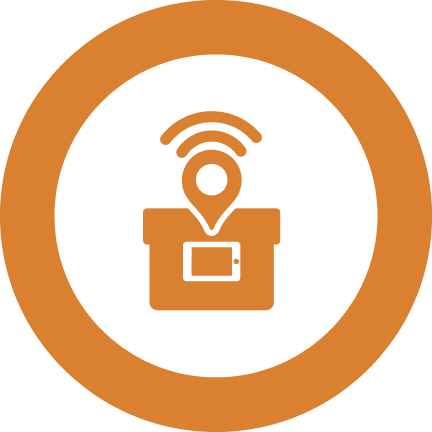
The Logiscend Difference
What makes Logiscend different than other Asset Tracking applications? It’s simple — our Container and Asset Tracking Application allows you to not only track your assets, but also provides you with the reporting and documentation you require to maintain your assets — as well as their records — to ensure compliance. Containers are the most effective way to transport materials through a manufacturing environment and will be the key to achieving Smart Materials — a core tenet of Industry 4.0, the IoT initiative for manufacturing. Logiscend breaks new ground with their “smart container” technology:
- Visual tags provide visual instruction for individual containers
- Hands-free, simple communication between “smart containers” and humans ensures higher quality and reduces errors.
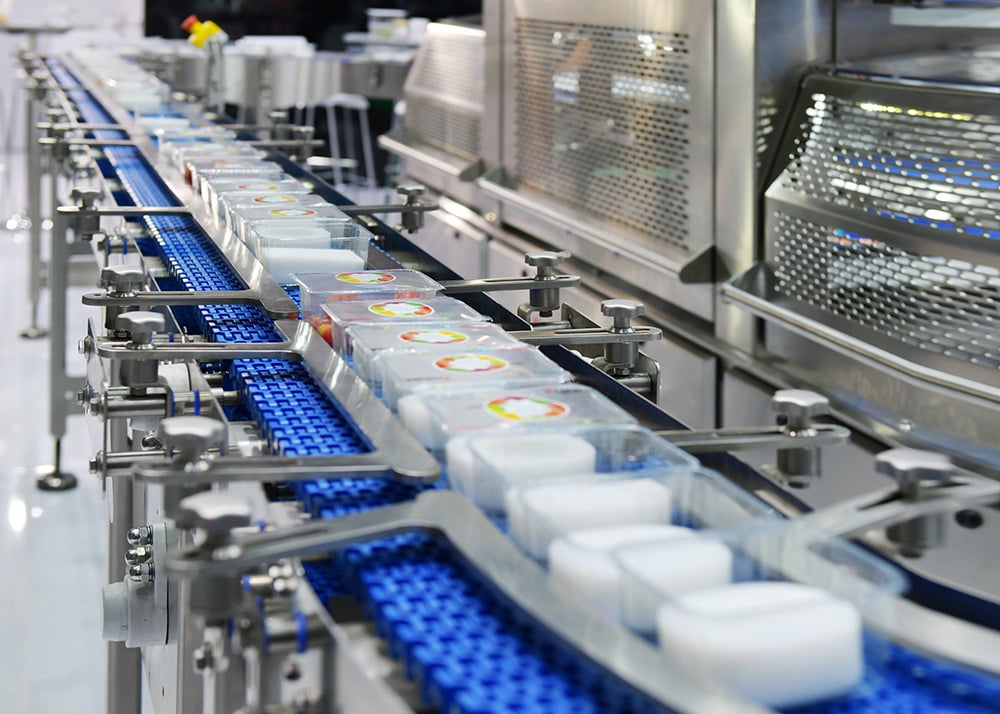
Customize and configure
- Fully configurable location and asset attributes
- Nested parent-child relationships
- Easily adapted to your branding colors/schemes
- Easily set user roles and access
- Data can be segmented based on group/department to assure secure data access
- Ability for users to create, edit and delete jobs with user defined attributes to perform a task. Users can define start/end timestamps, priority, state (ready, not ready, hold, complete). An audit log keeps track of all the changes to the job.
Scalable
- Import assets, set locations and connected devices
- One location to multiple sites
- Move and copy definitions for easy setup
- Secure socket implementation
- Support thousands of assets with a single Logiscend Container and Asset Tracking application
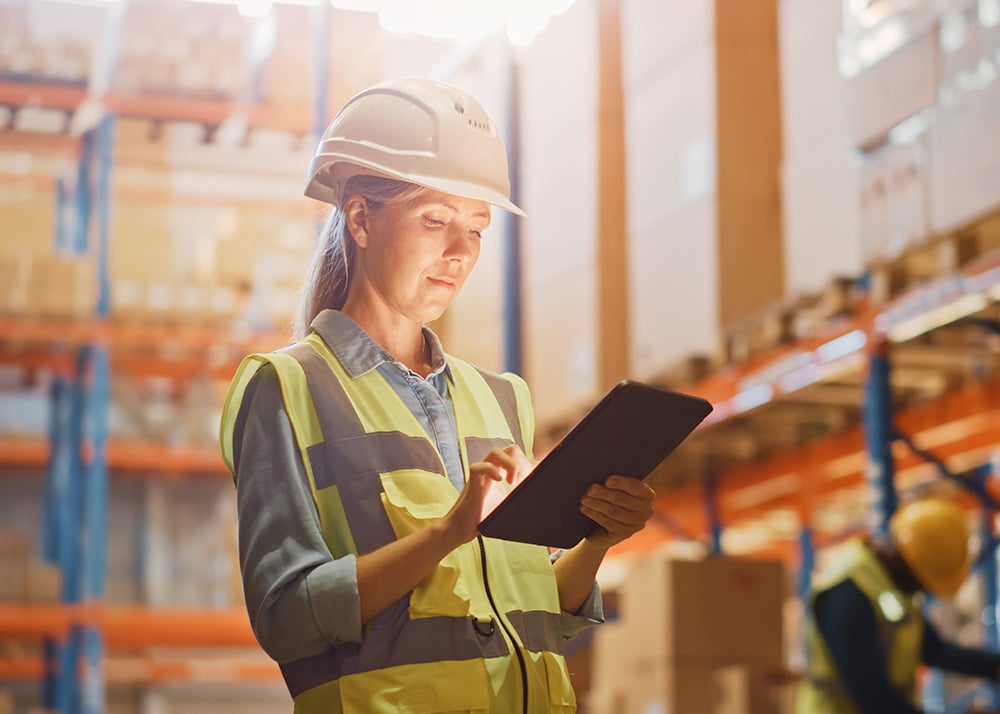
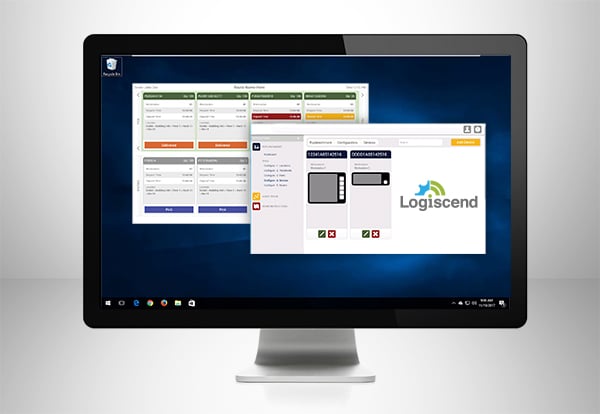
Customize reports and UI
- Export data to .xls to sort
- Utilize formatted reports such as assets by location or assets moved from one location to another
- Configure maps and geo-fenced locations to enable customized monitoring of assets and manufacturing workflows
- Dashboards provide location, delivery data and alerts to analyze process performance in real-time:
- Identify bottlenecks to improve throughput
- Balance processes and eliminate waste (Muda)
- Connect easily to existing ERP/MES/WMS systems
Mobility
- Commission and associate RFID & BLE tags
- Location ID
- Inventory workflow
- RFID locator function
- Full visibility and control of individual containers as they move through the process enables reallocation or re-direction as bottlenecks occur:
- Alerts operator when container has arrived at wrong location
- Counts empty containers and allocates to process stations in real time
- Self-directed or “smart containers” are location aware to provide real-time, accurate operator instruction based on each process step or work zone location:
- Little to no training or retraining is required — visual display tags tell operators exactly what to do
- A simple button push by operators begins a new job or verifies process completion
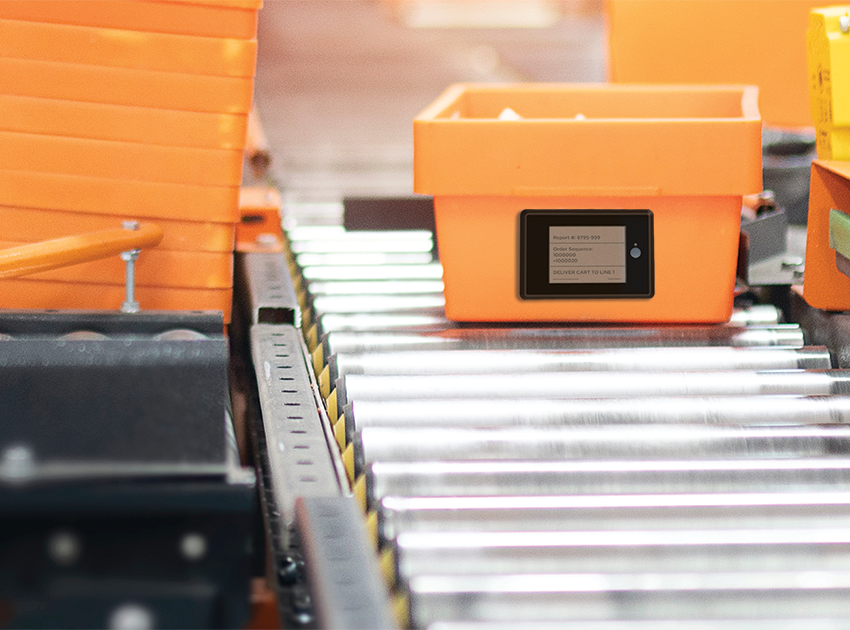
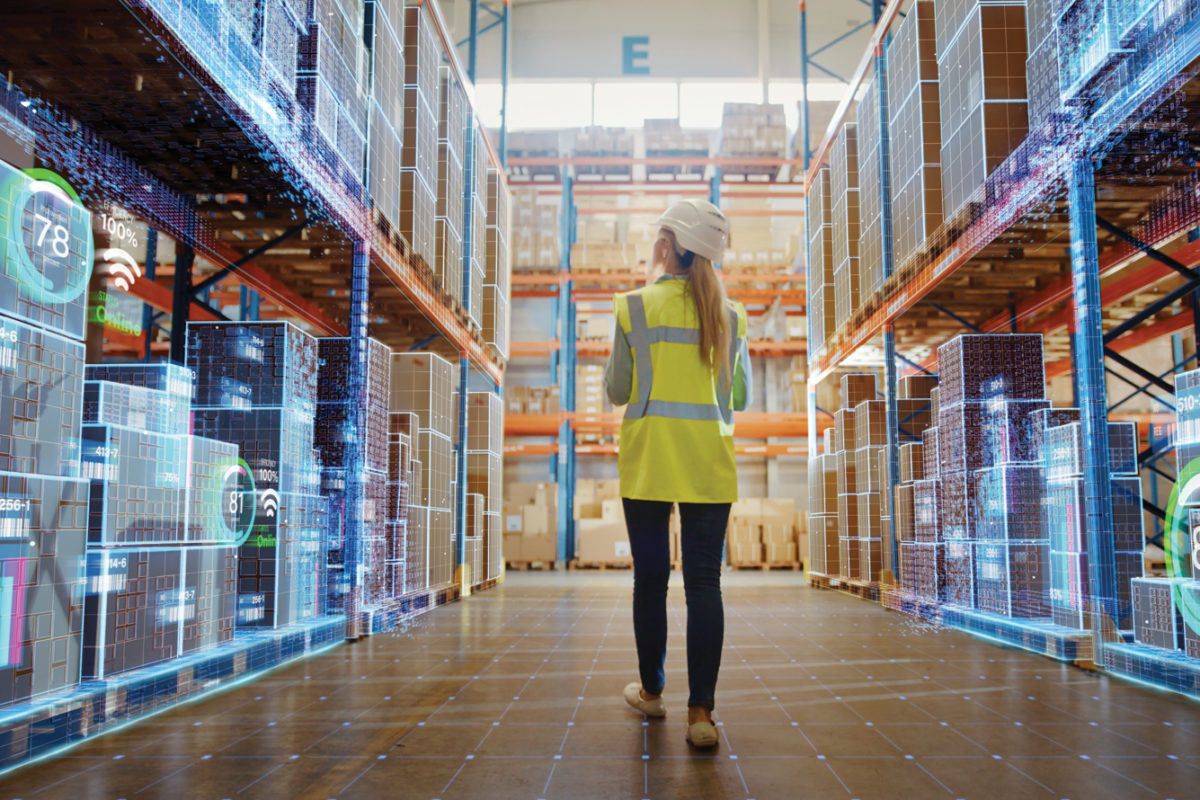
Open Architecture
- We will work with you to design the right tag solution for your application. The Logiscend software supports multiple industry standard RFID protocols including:
- EPC RFID Protocols Gen-2, ISO 18000-63 (info)
- RAIN RFID (UHF)
- Visual tags, passive RFID, active RFID, RTLS and many more commonly used communication technologies
- Integrations with industry leading RFID & RTLS providers:
- Impinj
- TSL
- Laird
- Omni-ID
- Others
Paper-based or other manual processes are highly error-prone and inefficient when it comes to locating your containers and ensuring they arrive at the correct destination with the proper process step.
The Panasonic Logiscend Smart Container Application automatically tracks, traces and logs containers — and any associated contents — as they move through your assembly process. Whether it’s finding an empty container to begin a job, delivering parts or completing a tool calibration, the Logiscend Container and Asset Tracking Application ensures you know where all your materials are at any time during the process.
Related content
Professional services
Panasonic is your trusted integrated solutions partner, committed to helping improve your organization’s key performance indicators (KPIs), including productivity, quality, and cost targets. Our ultimate goal — enterprise-wide operational excellence. We offer a full suite of services which can be individually customizable to provide all support necessary for a successful program.
Planning
Proper site planning and preparation is critical to large-scale equipment installation. From preliminary designs, to complete implementation specifications and solution testing, the Panasonic Logiscend Professional Service Group is ready to support your efforts. We will consult with you to understand your workflow, then design the right hardware and software solution for your facility. We can help you achieve your strategic objectives and assist in configuring a material flow management solution that meets your goals.
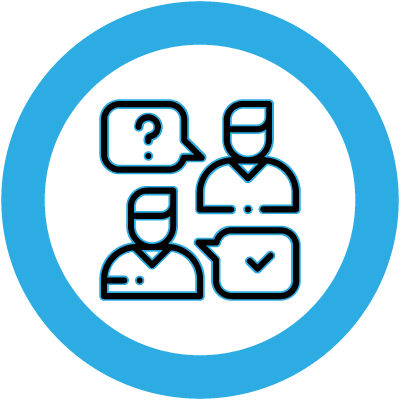
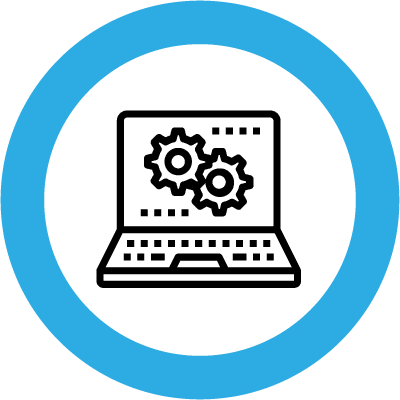
Installation & implementation
Our Installation & Implementation Services help you deploy the Logiscend System with minimal disruption. Services range from project management, hardware and software installation support, IT integration, system setup and configuration, user and administrator knowledge transfer and training, as well as user acceptance test supervision and documentation. We utilize the Project Management Body of Knowledge (PMBOK) guide and standards.
Maintenance & support
Our expert maintenance and support team are dedicated to maximizing your investment and helping you drive performance and usability. In addition to repair services, we offer remote equipment monitoring and preventive maintenance. Your annual subscription entitles you to the latest software releases ensuring you are up to date with new features and security enhancements.
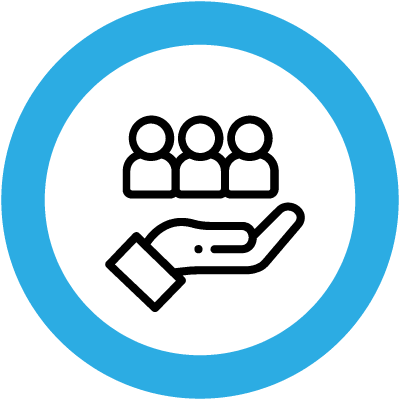
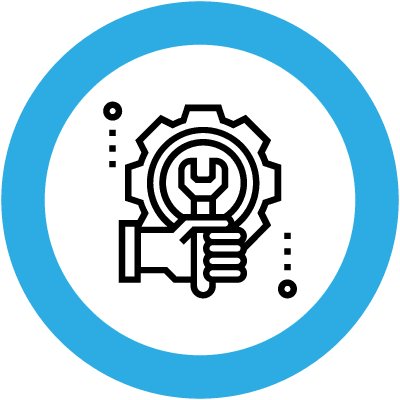
Engineering services
We have a team of experienced hardware and software engineers that can be deployed should your workflow require a unique implementation. We will work with your team to document scope, cost and an implementation timeline. If your organization has specific goals or conditions which must be met, our Engineering Services department will consult closely with your team to design and implement the best and most appropriate solution for your needs.

Are you looking for more information about Panasonic IIoTS solutions?
Our professional team is ready to help. Send your questions and a Solutions Engineer will contact you shortly.