Detroit Manufacturing Implements Panasonic Logiscend for Enhanced Material Flow Automation and Data Collection
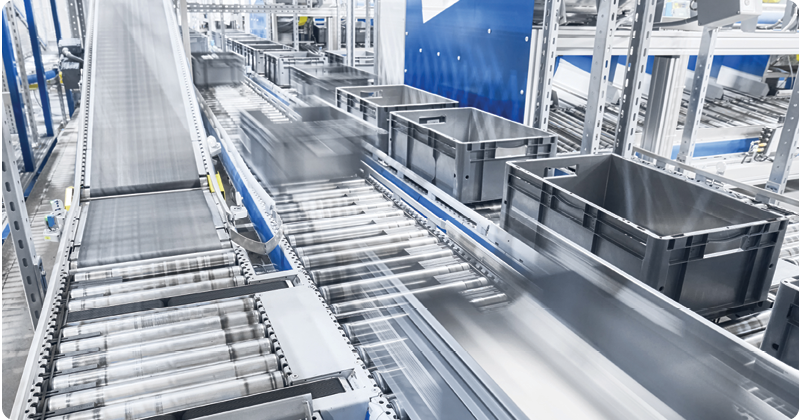
Customer Background
Detroit, a subsidiary of Daimler Trucks North America, has been a leader in heavy-duty commercial truck engine and chassis component manufacturing since 1938, serving prominent brands such as Freightliner and Western Star. In their Michigan facility, Detroit’s production line operates at full capacity, producing 170 engines per shift – a pace that demands highly efficient processes. As technology advances, the limitations of traditional paper-based systems, such as the Kanban card, have become evident, prompting Detroit to seek innovative solutions to optimize parts replenishment.
The Challenge
Detroit’s long-standing Kanban system presented several challenges, including manual part request handling, reliance on costly print materials, limited data collection, and an inability to provide real-time updates. These limitations impacted production line uptime and overall efficiency. To enhance productivity and streamline workflows, Detroit identified parts replenishment as a critical area for improvement. Key goals included:
- Eliminating parts outages to increase line uptime.
- Balancing workflows and improving driver allocation using data-driven insights.
The Solution
In response to these challenges, Detroit turned to the Panasonic Logiscend platform and engineering services. Leveraging intelligent integration and comprehensive data collection, Logiscend provides a robust, scalable platform that replaces traditional Kanban cards with View tags and RFID devices that enable real-time part order requests and status updates on the production floor.
Logiscend’s implementation team collaborated closely with Detroit to optimize system design and functionality, conducting on-site tests to map floor layouts and traffic flow. Through this tailored approach, Logiscend deployed a solution that enables Detroit to transition seamlessly to digital, integrated material flow automation.
Benefits of Logiscend for Detroit
Panasonic Logiscend's solution delivers real-time data collection from new sources, empowering Detroit to:
- Track material locations and status.
- Enhance communication with visual, human-readable instructions.
- Automate inventory management.
- Implement a scalable, flexible system capable of evolving with future automation needs.
The Results
Since implementing Logiscend, Detroit has realized significant benefits including:
- Reduced line interruptions and overtime, delivering measurable cost savings.
- Enhanced visibility into parts status and workflow processes.
- Improved communication between departments, facilitating shift transitions and workload balance.
- Access to real-time data on work-in-progress (WIP), allowing dynamic driver reallocation.
Panasonic Logiscend has empowered Detroit to transition from a paper-based system to a data-driven, intelligent supply chain that enhances productivity, scalability, and efficiency. This deployment illustrates Panasonic Logiscend's commitment to helping manufacturers seamlessly evolve their material flow automation through intelligent integration, added functionality, and robust data collection.