Increasing Accuracy and Efficiency On Automotive Production Lines
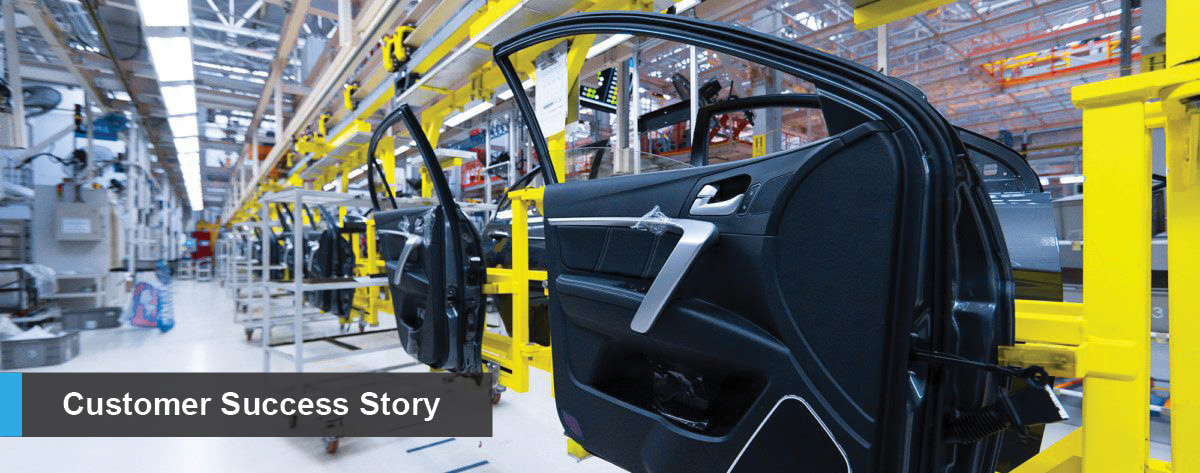
Customer Success Story
Complex production requirements are the mainstay of automotive manufacturing. While Henry Ford may have never actually said "Any color the customer wants, as long as it’s black" the general principle of manufacturing has always been that if you reduce the options, you can increase production and productivity while saving costs. The problem with that adage is that it does not consider the needs of today's customer and production line requirements.
The Challenge
A major automotive manufacturing plant located in the southern part of the United States came to us with a challenge. Their production line needed to support a wide variety of ever-changing vehicles and models, with hundreds of components and thousands of parts needed to support the sequences to keep the production line flowing. Their current material flow management system was a pick-to-light based system that while functional, the system was limited in several ways that impeded the production line productivity. The key challenges they faced centered around data management and access, hardware limitations and system support and services.
Data Collection
Using a traditional PLC based system generated challenges for gaining insight into line productivity. While real time data collection was possible, there were limitations on what data was collected and the data they had archaic and not easy to parse. The system provided limited instruction to the operator on current pick requirements and historical data was not stored or available for process improvement analysis.
Hardware Limitations
Each piece of hardware in the system had to be hardwired to a PLC. Each pick switch required wiring for power and functionality which made reconfiguration difficult and expensive. Model changes require frequent production line/process reconfiguration, and they needed a streamlined solution to manage this.
System Support and Flexibility
Without local support (the supplier was not North America based) issues would often take multiple days to connect with and obtain support on the phone, which crippled the production line With limited support for the features that they had There was no option to add new features to the system based on evolving production requirements.
The customer needed a flexible system (something that could grow and change as needs evolved, the ability to rapidly adapt to model changeovers without headache), and a US-based support system that was available to respond quickly and efficiently. In addition, they were eager to take advantage of the data collection features only a IoT based system could provide.
The Solution
Logiscend by Panasonic offered a unique solution to these challenges. With a platform based modular approach, Logiscend could tackle this one part of the manufacturing process without requiring significant downtime, an entire plant overhaul or drastic system changes.
“The Logiscend team was great to work with. Their production engineers collaborated closely with our team to ensure their solutions addressed key problems. Their US-based test lab allowed us the ability to make a huge amount of progress on the implementation without interrupting our active line activity.”
The automatic data collection provided by the Logiscend solution enables insight into the effectiveness and efficiency of the picking process of the production line identifying opportunities for cost savings and time efficiency. Logiscend was also able to collect the data on the location of the carts as they traveled from the pick station through the production line. Using this data, the customer was able to set up alerts that would notify key personnel if something were wrong. For example, a cart pulled offline mistakenly would at once be transparent.
Moving away from a PLC based system also allowed the data to be store in one central location, creating a baseline for the future as the customer extends the Logiscend platform for additional tasks. For the first time ever, the data from all picking areas in the plant could be compiled together for analysis.
Logiscend easily integrated with their existing hardware and systems and offered a flexible solution featuring wireless components for greater flexibility, digital readouts and work instructions that adapted to the container, location, and requirements at each stage of the process.
The Panasonic integration and support team worked extensively with the manufacturing team on the use case, adapting the Logiscend system to the customer needs so that model changes could happen in matter of minutes, rather than expensive reprogramming and rewiring that would need to occur in the past.
As the project evolved the support team help with a number of added workflow optimization features that were requested and implemented. The modular platform-based nature of Logiscend allowed for the core functionality to be built upon and customized to meet the customer’s exact needs.
The Results
Leveraging the existing features of the Logiscend platform's modular components allowed for rapid deployment of the first phase and did not require lengthy software development. The restful API interface integrated with our existing systems, reducing the need for complex integrations.
In our initial tests, the implementation ran in parallel with an existing pick to light legacy system allowing for a true comparison of the functionality. The overall benefits were significant and went well beyond expectations.
Not only did the processes run smoothly, but there were also significant improvements in employee productivity, and it simplified the training process. The digital displays provided consistent, updated, and accurate information to the line team and adapted to each part of the process.
Of course, the data collection component provided the biggest win. The Logiscend system tracked all the steps along the way and provided data that helped identify inefficiencies, reduced errors, and streamlined the processes overall.
Are you looking for more information about Panasonic IIoTS solutions? Our professional team is ready to help. Send your questions and a Solutions Engineer will contact you shortly.