Automated Kitting Solutions: Replenishment
Getting the right parts to the right place at the right time is essential in any factory
The Panasonic Logiscend Replenishment Application ensures your operators never run out of parts at any point in the process.
Parts replenishment is a key function in any manufacturing operation. The Panasonic Logiscend System allows an operator to “call” for parts or services by pressing a button on the visual tag, having the tag “auto call” via an optional sensor, or ordering parts with a tablet and immediately receiving a response via a “call sent” message right on the tag. The warehouse receives the message and executes the pick. Delivery is then scheduled via configurable routes and instruction is sent to the driver for pickup. The entire system is wireless, enabling low installation costs and quick reconfiguration for a dynamic factory. Ask our solutions engineers how this can work in your facility.
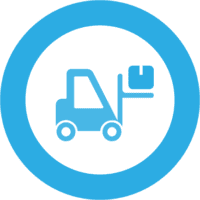
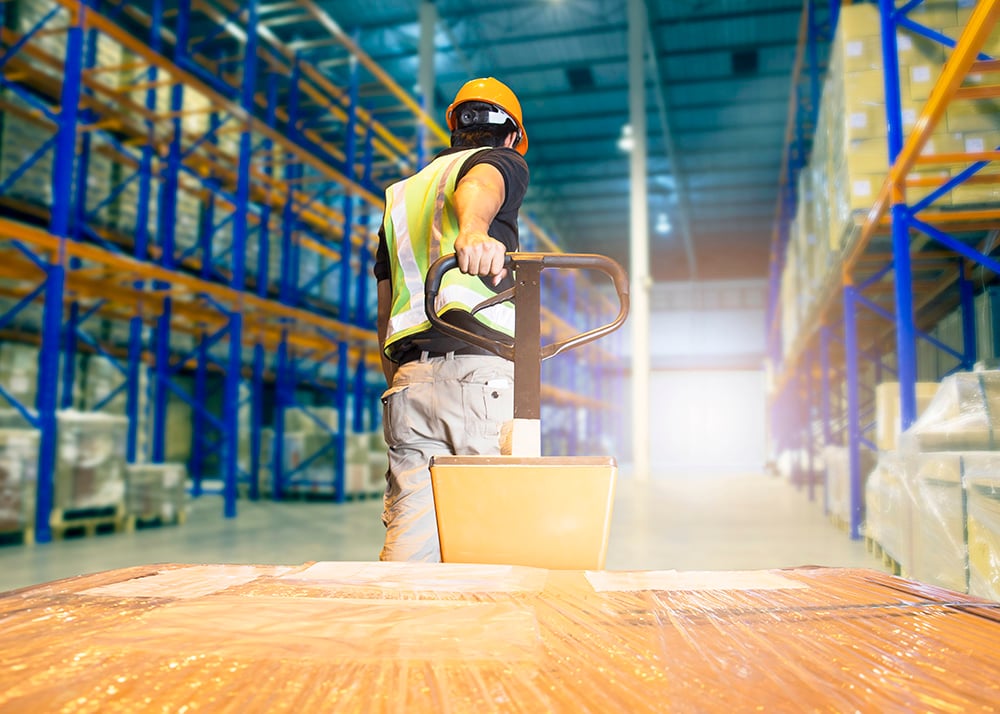
Standard work: No training or re-training necessary
This simple and intuitive system includes visual indicators and instruction right on the visual tag for the operator, warehouse and driver. Visual instruction and automatic driver routes require little to no training – providing for ease of use and deployment.
- Automated call is triggered when rack or bins are empty, eliminating opportunity for error in parts call
- Eliminates need for manual replenishment flags and material handler “searching”
- Increases employee retention rates with highly simplified system (less training required)
Re-configurability: Simple wireless deployment
The Logiscend system requires no wired infrastructure so it is easy to reconfigure or add in a part change on the fly – no IT involvement is necessary.
- Dynamic supermarket capability
- No hard-wired infrastructure is required, easy to reconfigure zones
- Reduces capital purchases, fewer racks and containers necessary
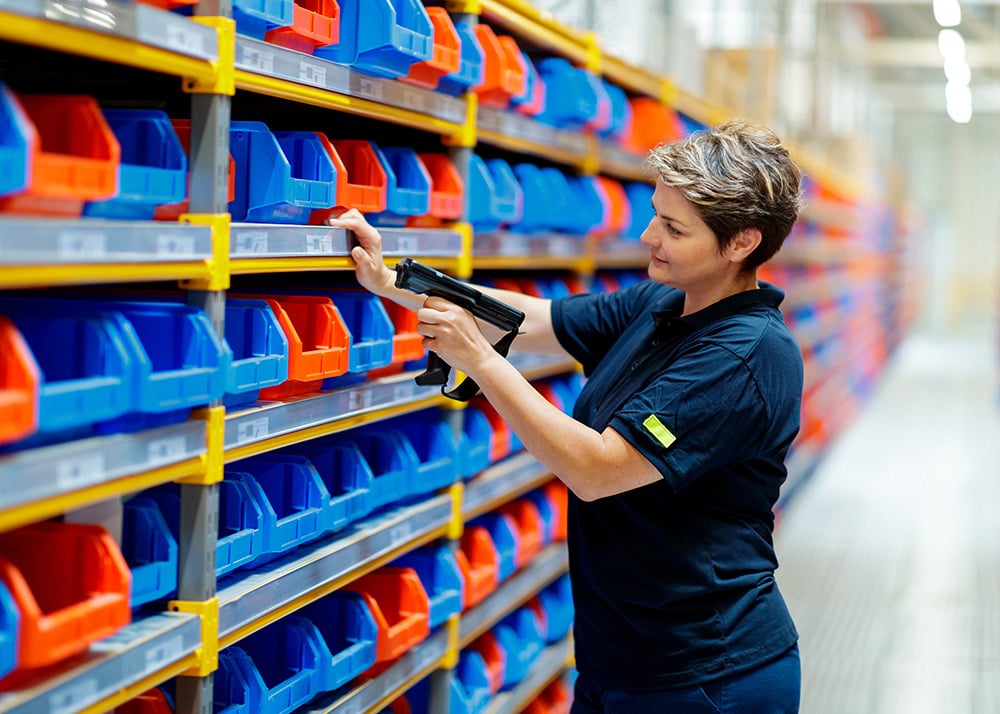

Monitor KPIs: Manager & driver dashboards
Logiscend requires no wired infrastructure. Unlike complex pick-to-light options, the Logiscend Pick Application provides simple installation and re-configurable where you need it — when you need it.
- Easily create temporary Pick locations based on demand and volume
- No hard-wired infrastructure is required, allowing
for line rebalancing
Logiscend combines the strengths of RF picking, visual logistics, and traditional pick-to-light systems to improve accuracy to 99.97%.
Professional services
Panasonic is your trusted integrated solutions partner, committed to helping improve your organization’s key performance indicators (KPIs), including productivity, quality, and cost targets. Our ultimate goal — enterprise-wide operational excellence. We offer a full suite of services which can be individually customizable to provide all support necessary for a successful program.
Planning
Proper site planning and preparation is critical to large-scale equipment installation. From preliminary designs, to complete implementation specifications and solution testing, the Panasonic Logiscend Professional Service Group is ready to support your efforts. We will consult with you to understand your workflow, then design the right hardware and software solution for your facility. We can help you achieve your strategic objectives and assist in configuring a material flow management solution that meets your goals.
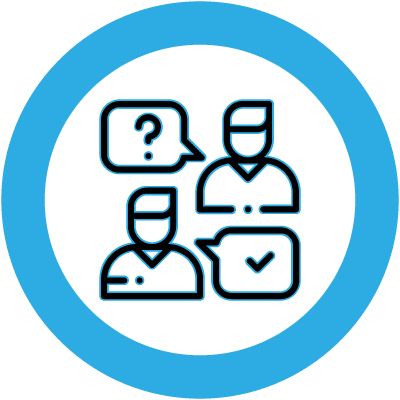
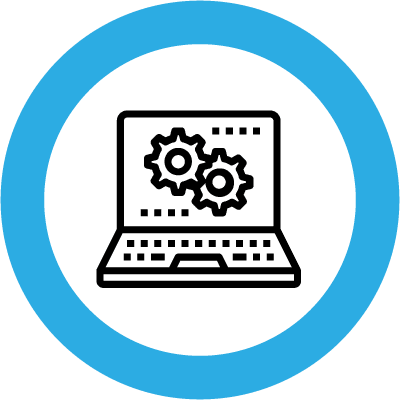
Installation & implementation
Our Installation & Implementation Services help you deploy the Logiscend System with minimal disruption. Services range from project management, hardware and software installation support, IT integration, system setup and configuration, user and administrator knowledge transfer and training, as well as user acceptance test supervision and documentation. We utilize the Project Management Body of Knowledge (PMBOK) guide and standards.
Maintenance & support
Our expert maintenance and support team are dedicated to maximizing your investment and helping you drive performance and usability. In addition to repair services, we offer remote equipment monitoring and preventive maintenance. Your annual subscription entitles you to the latest software releases ensuring you are up to date with new features and security enhancements.
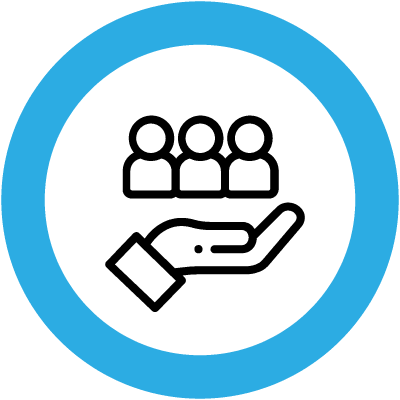
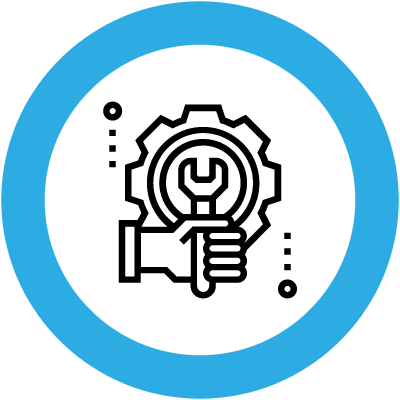
Engineering services
We have a team of experienced hardware and software engineers that can be deployed should your workflow require a unique implementation. We will work with your team to document scope, cost and an implementation timeline. If your organization has specific goals or conditions which must be met, our Engineering Services department will consult closely with your team to design and implement the best and most appropriate solution for your needs.
Are you looking for more information about Panasonic IIoTS solutions?
Our professional team is ready to help. Send your questions and a Solutions Engineer will contact you shortly.