Work Instructions
Make an exponential leap forward in cost savings, quality and the ability to manage complexity in modern manufacturing
The Logiscend Work Instructions Application eliminates paper and provides the ability to deliver the right instructions to the right work zone every time. And the instructions can be dynamically updated for changes in production or process.
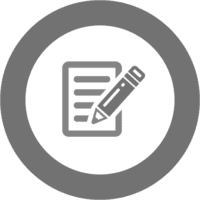
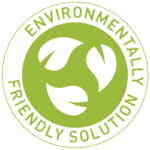
Efficient process workflows are the key to ensuring a seamless operation. The Work Instructions Application eliminates paper and provides the ability to send the appropriate instruction to a monitor or tablet on the factory floor to instruct the operators automatically. As a part arrives in the work cell, the build or work instructions are displayed via a web browser. With our Bluetooth Low Energy (BLE) RTLS tags on your material work instructions can be triggered based on position changes of less than 1 meter*. Content can be easily created or edited to meet changing production demands. Talk to a solutions engineer to explore solutions for your production facility.
- Provide dynamic instructions based on locations (changes of less than 1 meter* can be detected with BLE tags)
- Deliver instant quality or hold instructions
- Re-route materials to respond to changes in workflow
- Enable faster productivity in temporary workforces and enhanced procedure compliance
- Create standardized processes that decrease the defect rate
- Provide dynamic instructions based on locations (changes of less than 1 meter* can be detected with BLE tags)
- Deliver instant quality or hold instructions
- Re-route materials to respond to changes in workflow
- Enable faster productivity in temporary workforces and enhanced procedure compliance
- Create standardized processes that decrease the defect rate
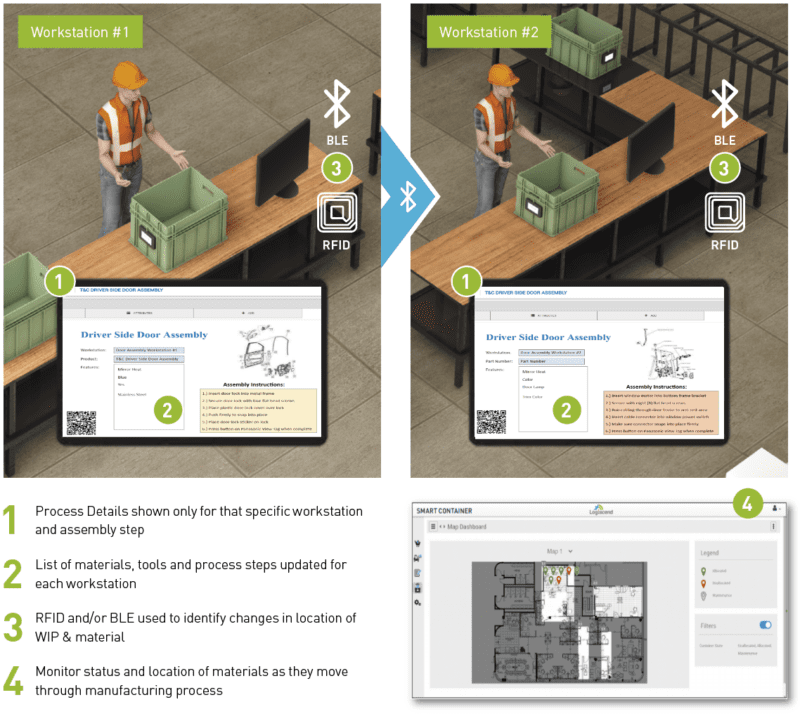
Related content
Professional services
Panasonic is your trusted integrated solutions partner, committed to helping improve your organization’s key performance indicators (KPIs), including productivity, quality, and cost targets. Our ultimate goal — enterprise-wide operational excellence. We offer a full suite of services which can be individually customizable to provide all support necessary for a successful program.
Planning
Proper site planning and preparation is critical to large-scale equipment installation. From preliminary designs, to complete implementation specifications and solution testing, the Panasonic Logiscend Professional Service Group is ready to support your efforts. We will consult with you to understand your workflow, then design the right hardware and software solution for your facility. We can help you achieve your strategic objectives and assist in configuring a material flow management solution that meets your goals.
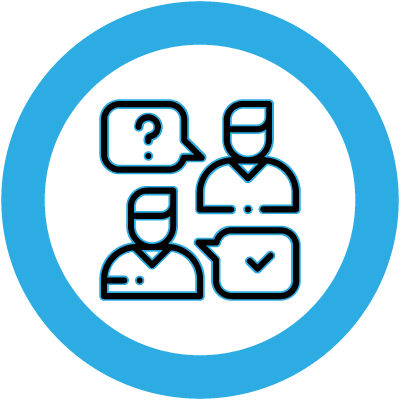
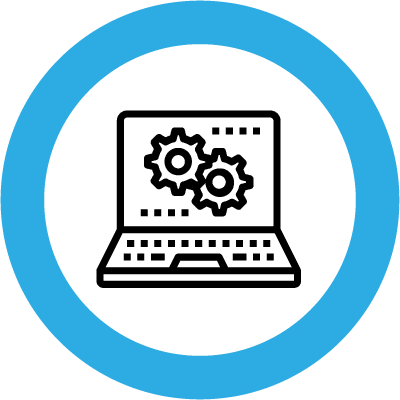
Installation & implementation
Our Installation & Implementation Services help you deploy the Logiscend System with minimal disruption. Services range from project management, hardware and software installation support, IT integration, system setup and configuration, user and administrator knowledge transfer and training, as well as user acceptance test supervision and documentation. We utilize the Project Management Body of Knowledge (PMBOK) guide and standards.
Maintenance & support
Our expert maintenance and support team are dedicated to maximizing your investment and helping you drive performance and usability. In addition to repair services, we offer remote equipment monitoring and preventive maintenance. Your annual subscription entitles you to the latest software releases ensuring you are up to date with new features and security enhancements.
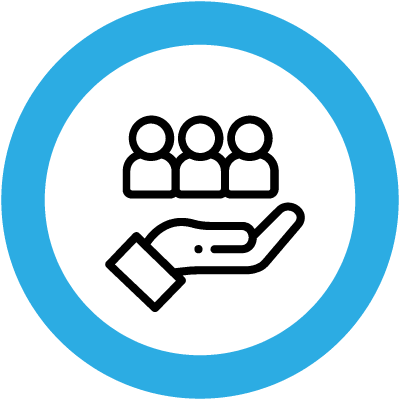
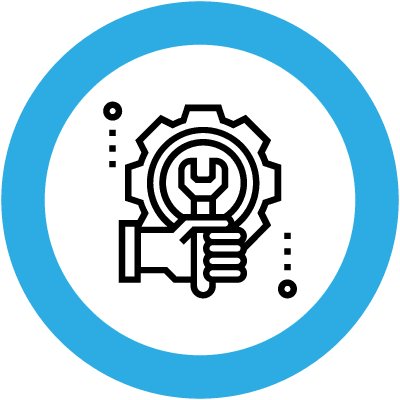
Engineering services
We have a team of experienced hardware and software engineers that can be deployed should your workflow require a unique implementation. We will work with your team to document scope, cost and an implementation timeline. If your organization has specific goals or conditions which must be met, our Engineering Services department will consult closely with your team to design and implement the best and most appropriate solution for your needs.
