The Logiscend™ System
One platform to handle all material flow
In our view, technology should move us all forward. It should enable us to create abundance out of scarcity, power the things that make our work easier, and energize our perpetual ambition for progress. These viewpoints all converge with the creation of Logiscend™ — the world’s first universal platform for material flow management.
With Logiscend, you can trace your assets and containers in real time through the entire manufacturing network for complete process visibility. You can train your workers more quickly and enable them to work more accurately. You can reduce line downtime with timely replenishment and faster picking. You can easily reconfigure lines with our wireless hardware. And you can do it with the solid backing of Panasonic — one of the world’s preeminent innovators in advanced manufacturing, digital technology and industrial automation.
And all of this with easy start, small investment, and full integration with your corporate ERP/MES systems. Talk to our team for details.
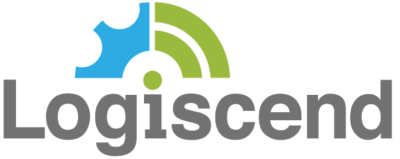
Solutions and Applications
Kitting Process Solutions
The Logiscend Pick Application reduces errors and increases picking speed by providing visual cues and instruction for operators with a wireless display tag on each bin, rack or shelf. The Replenishment Application allows operators to call for parts or services by pressing a button on the display tag — Admin and driver dashboards provide visibility into calls and deliveries.
Container Management Flow
The Asset Tracking Application allows yWork Instructionsou to trace assets, automate WIP inventory and check in/out of tools, ensure up-to date inventory, asset maintenance and compliance across all of your locations utilizing RFID. The Smart Container Application automatically tracks, traces and logs containers — and any associated contents — as they move through your assembly process.
Work Instructions
The Work Instructions Application sends dynamic work instructions to the display tags or monitors on the factory floor to instruct operators automatically, based on location and process flow — ensuring the correct instruction is always provided at the right workstation.
Why Logiscend
The Logiscend platform for paperless material flow management is designed to supercharge your plant’s efficiency. With this in mind, we focused on improving five key areas in the enterprise manufacturing process: Pick, Replenishment, Asset Tracking, Smart Container, and Work Instructions.
Ask our engineers why Logiscend is the best solution for your plant.
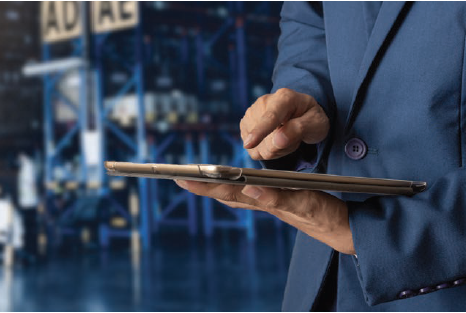
Automated Kitting Solutions
The Pick Application is designed for simplicity of process:
- Little training is required, so even temp workers can be used
- Our visual cues lead to reduced errors, especially for just-in-sequence assembly
- Dynamic tags promote faster picking and less downtime, far more benefits than Pick-to-Light
The Replenishment Application helps reduces workforce requirements:
- Eliminate the need to have workers walking the line to check inventory
- Interactive software streamlines the replenishment delivery process
- Tighter inventory control and management due to real-time, need-based parts delivery
Download Kitting Solutions brochures:
Container Flow Management
The Container and Asset Tracking Application is engineered to eliminate wastage through increased visibility, dramatically reducing the 20% of standard containers reported lost on an annual basis:
- Passive and active RFID tags provide location and line metrics throughout your facilities
- It is flexible: for inventory manufacturing it provides process visibility; for custom manufacturing it provides product visibility
- It is plug-and-play: Logiscend software integrates with existing systems, so you don’t have to configure tracking capabilities
- The application automatically tracks, traces and logs containers and contents as they move through the assembly process
- It alerts operators if a container arrives at the wrong location
- The application counts empty containers and allocates them to process stations in real time
Download Container Flow Management brochures:
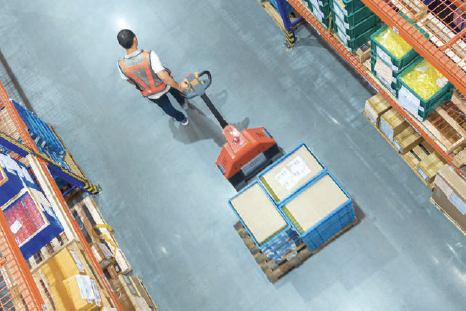

Work Instructions
The Work Instructions application is designed to increase efficiency:
- Dynamic tags display the correct work instructions based on location
- Tags can display new instructions by individual rack or container if issues arise
- The wireless tags track the Quality Assurance process and automatically count inventory for WIP items
The right place at the right time
We have worked hard to build a common platform for enterprise manufacturing. We believe that the Logiscend system creates a new paradigm for the manufacturing process:
- the visual cues of paper labels — without the paper
- the ability to trace assets and containers — with full process visibility.
- powerful Industrial IoT software platform to enable the digitization and manufacturing optimization of Industry 4.0.
And at the end of the shift, your assets will be in the right place at the right time to position your factory for even greater success. Contact our Solutions Engineers to start a discussion.
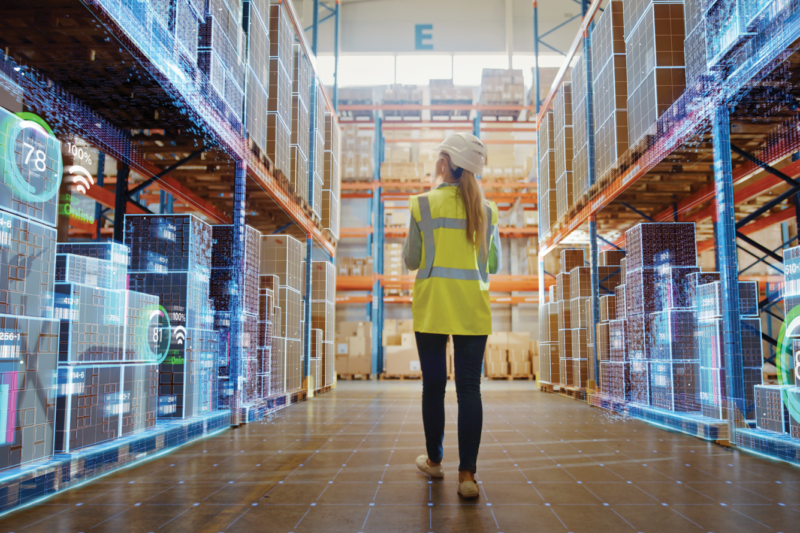